Cylinder Head Factory: Unveiling the Essentials of Diesel Engine Parts
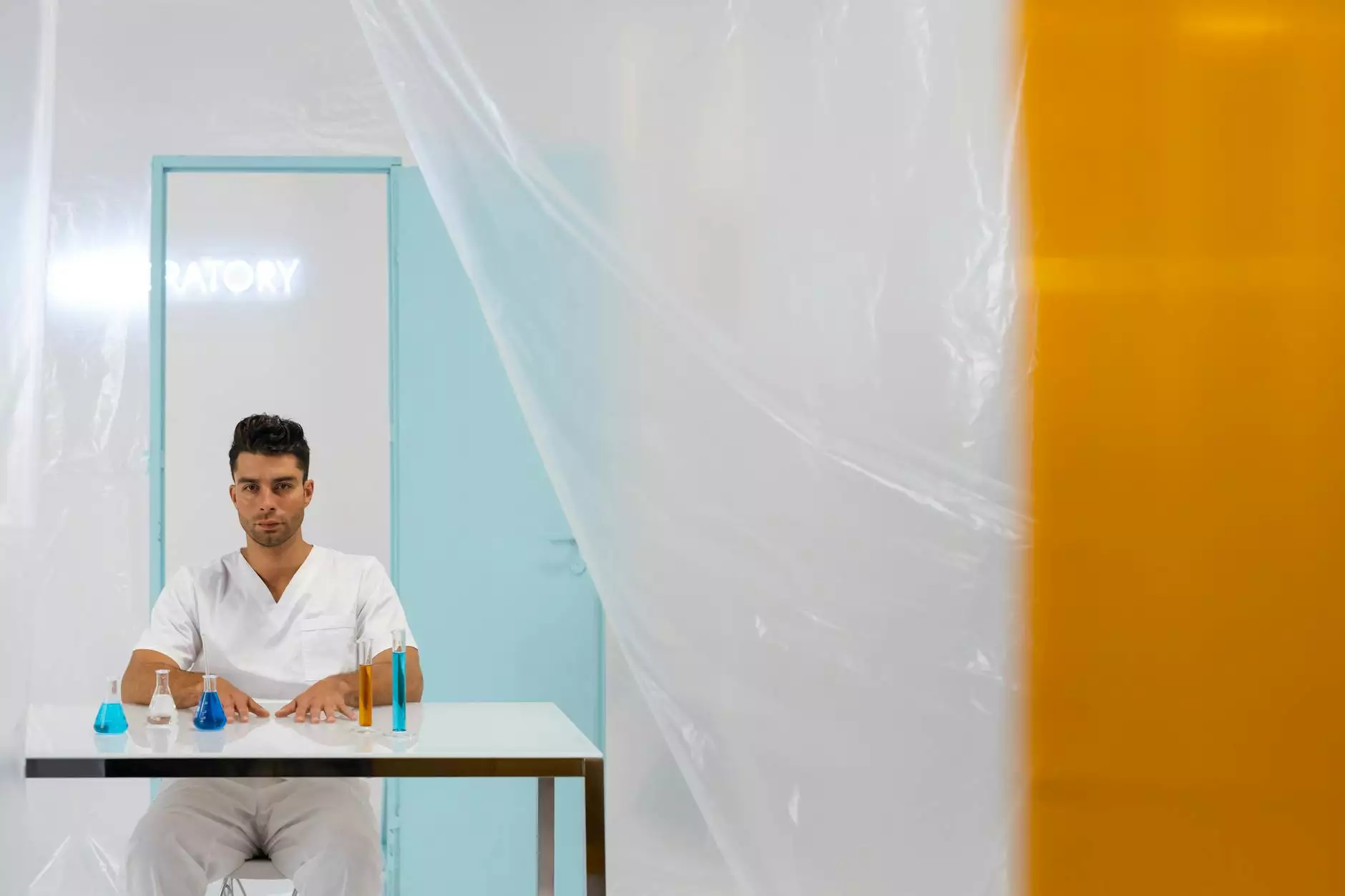
In the realm of diesel engines, the cylinder head factory plays a crucial role in the overall performance and efficiency of vehicles. A cylinder head is an integral component that houses critical parts of the engine, influencing everything from air intake to exhaust flow and engine cooling. This comprehensive article delves into the significance of cylinder heads, the operations of a cylinder head factory, and how they contribute to the field of diesel engine parts and spare parts supply.
The Importance of Cylinder Heads in Diesel Engines
Cylinder heads serve as the crown of the engine's combustion chamber, sealing the top of the engine block and containing features that are vital for engine operation. It is essential to understand why cylinder heads are paramount in diesel engines:
- Airflow Management: Cylinder heads facilitate the precise flow of air into the combustion chamber. This is critical for efficient combustion, which significantly affects power output and fuel efficiency.
- Fuel Injection: Many modern diesel engines utilize direct injection, where the injector is situated inside the cylinder head, directly influencing combustion dynamics.
- Heat Dissipation: Cylinder heads are designed to manage and dissipate heat produced during combustion, thus preventing engine overheating and ensuring longevity.
Understanding the Cylinder Head Factory
A cylinder head factory is a specialized facility dedicated to the manufacturing, reconditioning, and distribution of cylinder heads for diesel engines. These factories employ advanced technologies and stringent quality control measures to produce reliable and durable components. Here are some key aspects of how a cylinder head factory operates:
1. Manufacturing Processes
The manufacturing of cylinder heads involves several highly technical processes:
- Aluminum and Iron Casting: Most cylinder heads are made from either aluminum or iron, chosen for their heat resistance and weight. The casting process requires precision to create the mold accurately.
- Machining: After casting, cylinder heads go through a machining process to ensure they meet exact specifications. This step includes milling, drilling, and surfaces grinding.
- Quality Assurance: Each cylinder head undergoes rigorous testing to check for defects. Testing might include pressure tests to ensure there are no leaks and material integrity assessments.
2. Reconditioning Services
Cylinder head factories often provide reconditioning services, extending the life of existing cylinder heads. The reconditioning process includes:
- Cleaning: The removal of carbon deposits and contaminants through specialized equipment.
- Valves and Seats Replacement: Worn valves and seats are replaced to restore optimal performance.
- Surface Grinding: Ensuring a flat surface for proper sealing when installed back on the engine.
3. Research and Development
Innovation is vital in the automotive industry, and a cylinder head factory invests in research and development to enhance performance and efficiency. This may involve:
- Material Science: Developing composite materials that improve durability and reduce weight.
- Aerodynamics: Refining designs to optimize airflow within the combustion chamber.
Why Choose Quality Cylinder Head Suppliers
The choice of cylinder head and parts suppliers can significantly influence engine performance and reliability. Here are important factors to consider when selecting a supplier:
1. Reputation and Experience
Ensure that the supplier has a solid reputation in the industry. Look for reviews, case studies, and testimonials that highlight their experience with diesel engine parts.
2. Product Range
A reputable supplier should offer a wide range of cylinder heads and related spare parts. This diversity ensures that you can find the right components for various engine types.
3. Quality Certifications
Certification from recognized international standards, such as ISO 9001, indicates that the supplier maintains high-quality manufacturing processes.
Future Trends in Cylinder Head Manufacturing
The cylinder head industry is experiencing significant transformations driven by advancements in technology and changing regulations. Here are some emerging trends:
- Emissions Control: With stricter environmental regulations, future cylinder head designs will focus on improving emissions performance. Manufacturers are exploring new technologies to accommodate various fuel sources.
- Electric and Hybrid Solutions: As the automotive industry shifts toward electrification, cylinder head factories are diversifying their product offerings to include components for hybrid engines.
Conclusion
The cylinder head factory represents a cornerstone in the production and supply of diesel engine parts, offering vital components that directly influence performance and efficiency. By choosing the right suppliers and understanding the manufacturing processes, businesses in the automotive sector can ensure that they utilize the best available technology for their engines.
In a market that is continually evolving, staying informed and adapting to emerging trends will empower suppliers and manufacturers alike to thrive in a competitive landscape. With enhancements in materials, designs, and manufacturing processes, the future of cylinder head factories promises to bring even greater advancements in automotive technology.