The Essential Guide to Parts of CNC Lathe for Metal Fabricators
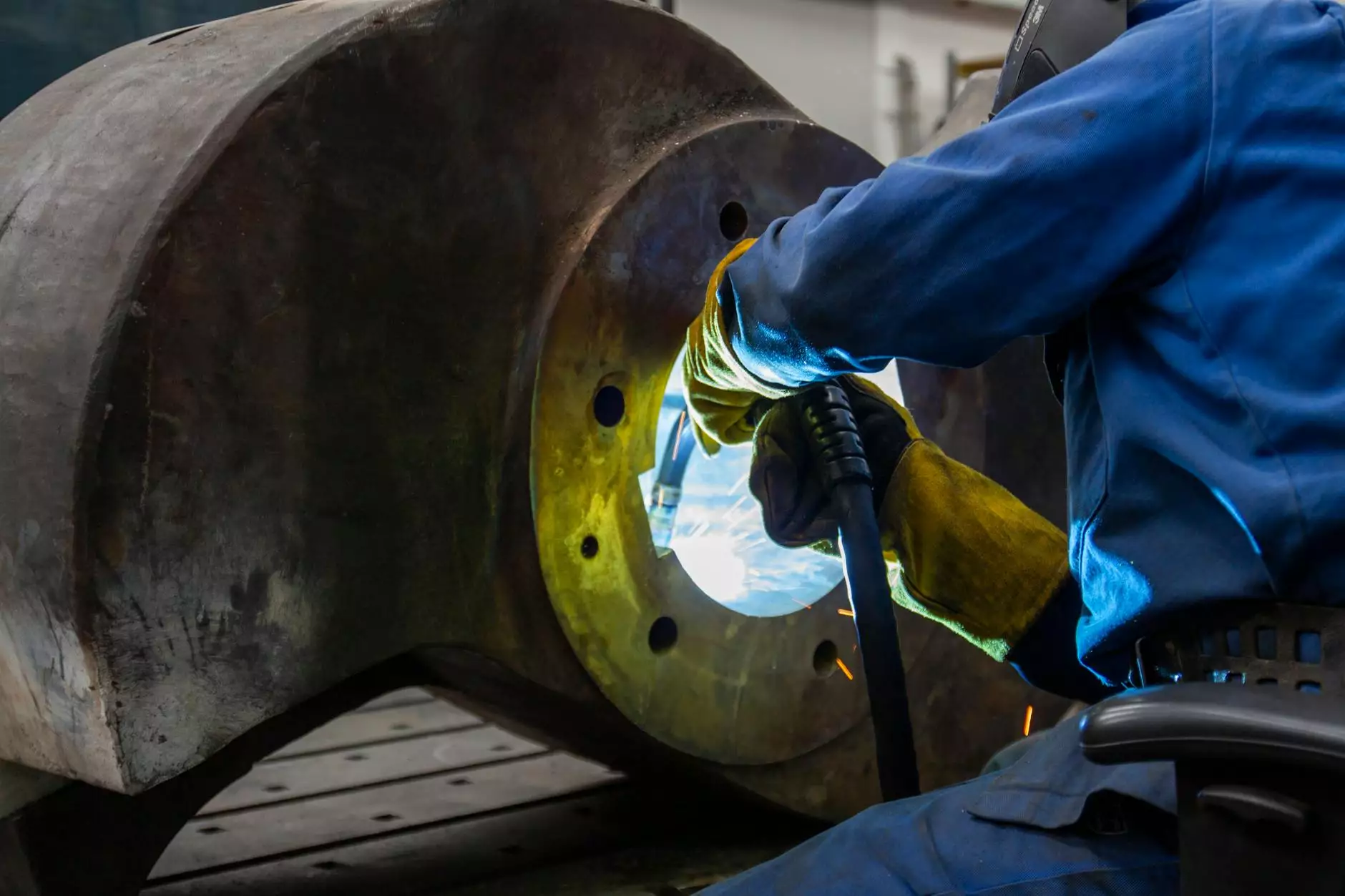
When it comes to metal fabrication, the tools and machines you use can significantly dictate the quality and precision of your projects. Among the most vital machines in a metal fabrication workshop is the CNC lathe. Understanding the various parts of CNC lathe machines is crucial for any fabricator who wants to enhance efficiency and accuracy in their work. This article provides a detailed exploration of these components, their functions, and their significance in the field of metal fabrication.
What is a CNC Lathe?
A CNC (Computer Numerical Control) lathe is a sophisticated machine tool that automates the process of shaping material such as metal. By utilizing pre-programmed software, CNC lathes can execute complex designs with high precision. This eliminates much of the manual labor associated with traditional lathe operations, allowing for greater production rates and enhanced consistency.
Key Parts of a CNC Lathe
To fully appreciate the functionality of a CNC lathe, it is essential to understand its various components. Here’s a rundown of the primary parts of CNC lathe machines:
1. Headstock
The headstock is one of the most crucial parts of a CNC lathe as it houses the spindle, which drives the rotating workpiece. Typically located at the rear of the machine, the headstock contains the following elements:
- Spindle: This is the rotating axis that holds the workpiece in place and turns it during the machining process.
- Motor: The headstock includes the motor that provides power to the spindle, enabling the lathe to handle various materials and shapes.
- Gears: These components allow for the adjustment of the spindle speed, providing flexibility for different machining operations.
2. Tailstock
Located opposite the headstock, the tailstock provides support for the workpiece at its non-driven end. It can be moved along the bed of the lathe for accommodating longer pieces. Key elements of the tailstock include:
- Centre: Typically accommodates a live center or dead center, helping to stabilize the workpiece during machining.
- Quill: Allows for height adjustment and can be retracted or extended as needed for different machining tasks.
3. Bed
The bed is the foundational structure of the lathe, designed to support the other components. It provides rigidity and stability during operation. Important features of the bed include:
- Guideways: These are precision-ground surfaces that allow the carriage and tailstock to move smoothly along the lathe.
- Material: Typically made from cast iron or other robust materials to withstand vibrations and stresses during machining.
4. Carriage
The carriage assembly is responsible for moving the cutting tool into position. It consists of several parts that work in tandem:
- Cross Slide: This component allows for lateral movement of the cutting tool, enabling precise adjustments during operation.
- Compound Slide: This slide provides additional angular adjustments, allowing for angled cuts and complex machining tasks.
5. Tool Post
The tool post secures the cutting tools in place, allowing them to be easily changed out as needed. Different types of tool posts can be used, including:
- Fixed Tool Post: Provides a stable and secure mount for the tool but limits flexibility in adjustments.
- Adjustable Tool Post: Allows users to make precise adjustments to the tool position, improving overall machining accuracy.
6. Control System
The control system of a CNC lathe is what differentiates it from traditional lathes. The system consists of hardware and software components that automate the machining process. Key features include:
- Computer or Controller: This is the brain of the CNC lathe, where the programming and commands are entered.
- Software: CAD/CAM software is used for designing parts and generating the necessary code for machining.
7. Chuck
The chuck is the part of the lathe that holds the workpiece securely in place. There are various types of chucks, including:
- Three-Jaw Chuck: Commonly used for gripping round workpieces, it self-centres as it closes.
- Four-Jaw Chuck: Provides greater versatility for gripping irregularly shaped workpieces but requires more setup time.
8. Feeding System
The feeding system is responsible for moving the workpiece or cutting tool incrementally. Key elements include:
- Lead Screw: This component facilitates the movement of the carriage, allowing tools to cut the material with precision.
- Feed Rod: Works alongside the lead screw to provide additional control over the tool’s movement speed.
The Significance of Understanding the Parts of CNC Lathe
For any metal fabricator, a thorough knowledge of the CNC lathe is essential. Understanding the individual parts of CNC lathe machines allows fabricators to:
- Optimize Performance: Knowing how each component works helps in diagnosing issues and enhancing machine performance.
- Improve Maintenance: Regular maintenance is crucial for prolonging the life of the machine, and understanding the components facilitates more effective upkeep.
- Enhance Machining Techniques: A deep knowledge of how the parts work together can lead to improved techniques and overall production quality.
Common CNC Lathe Applications in Metal Fabrication
CNC lathes are utilized for a myriad of applications in metal fabrication. Their versatility enables them to handle various materials and produce complex designs. Some common applications include:
- Turning: The primary function of CNC lathes, where material is machined into cylindrical shapes.
- Thread Cutting: Producing precise threads on screws and bolts.
- Drilling: Creating holes in metal parts with accuracy and consistency.
- Cutting: Shaping materials to specific designs and dimensions.
Conclusion
Understanding the parts of CNC lathe machines is fundamentally important for metal fabricators aiming for precision and efficiency in their work. Each component plays a critical role in the operation of the lathe, and without a thorough understanding, one may overlook its potential capabilities. As the manufacturing industry continues to evolve, embracing the technological advancements of CNC machinery will place fabricators at the forefront of innovation. Investing in knowledge of CNC lathe parts not only enhances production processes but also solidifies a fabricator's reputation for quality and accuracy in metal fabrication.